Is Compliance a Waste?
- Raimund Laqua
- Aug 6, 2018
- 2 min read
Updated: Sep 20, 2023
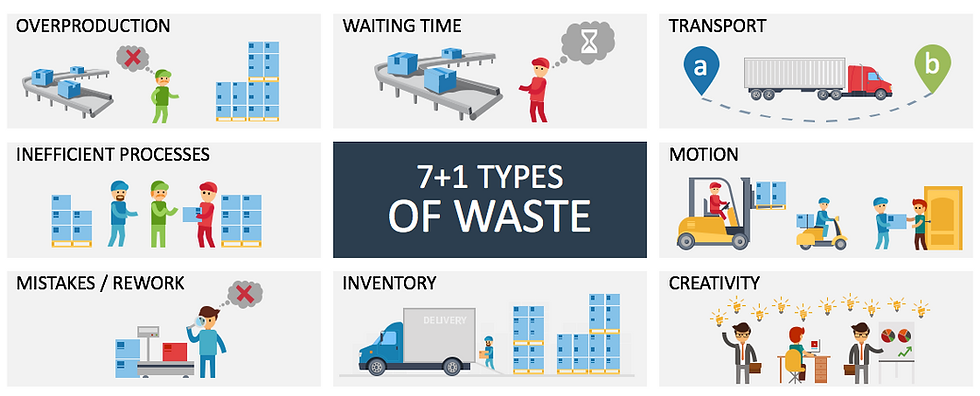
The value stream is where value is created but also waste which erodes the value of the products and services we are delivering. At a fundamental level, LEAN is about satisfying customer requirements with the least amount of waste as possible. By applying LEAN principles and practices organizations protect value by reducing or eliminating this waste.
There are many forms that waste manifests itself within a value stream. The most common include:
Overproduction – production that is more than needed or before it is needed
Inefficient processes – more work (or quality) required by the customer
Mistakes / rework – efforts caused by rework, scrap, or incorrect information
Waiting – wasted time waiting for the next step in the process
Inventory – excess products and materials not being processed
Transport – unnecessary movements of products and materials
Motion – unnecessary movements by people
Creativity – non-utilized talent
However, this list doesn't end there.
We know that customers are only willing to pay for the work that directly contributes to the creation of value. This is why many companies view compliance, particularly in the form of inspection, as a form of waste because it is seen as not directly contributing to satisfying customer requirements. Specifically, compliance adds to waiting, unnecessary movements, and to inefficient processes. These are indeed wastes when looked at in this way. But is this the best way to think about compliance – as a waste?
Customers do expect that companies build their products in accordance with regulations and standards. They expect that the environment will not be harmed, employees not injured, and that companies operate according to the rule of law and within ethical guidelines. If you don't believe this then eliminate risk & compliance functions from your organization and see what happens.
These expectations are as much customer requirements as are product or service requirements. Meeting compliance expectations creates legitimacy, trust and ultimately customer loyalty. These create value and without them it does not matter if you eliminate all the other forms of waste or reduce your cycle times to the lowest that they can possible go.
As we know customers will only pay for those things that contribute to value and that includes the outcomes of compliance: safety, quality, environmental, privacy and other stakeholder expectations. Customers refuse to buy products or services or even work for companies that choose not to meet their compliance obligations. In fact, they value companies with higher standards over those that only conform to the minimum from a legal perspective.
When companies consider compliance as a necessary evil they tend to use mostly inspections and audits which can contribute to waste in the value stream.
However, when compliance is seen as a necessary good, it is included as part of customer requirements. When this happens companies design compliance into their products and services as well as the processes that create them. This not only eliminates "waste" but also creates added value that results in reduced risk, increased trust, and sustainable growth through increased customer loyalty.