Does Compliance Hinder Innovation?
- Raimund Laqua
- May 10, 2017
- 3 min read
Innovation is necessary for growth and often requires that risks are taken. However, a common sentiment is that compliance is getting in the way. Compliance is taking away our ability to innovate and to be profitable. This is not only heard for new business development but also when changes are made to existing operations.
The pharmaceutical sector is one of the most regulated in industrialized countries. FDA has strict requirements for verification and validation of products and services. The risks to patients are many so it makes sense to scrutinize every aspect from design to delivery of new products. Changes made during the product life-cycle can lead to re-validation and conducting more clinical trials all of which introduce delays to the introduction of the new drug or medical device.
In 2005, the Quality Risk Management program ICH-Q9 was introduced to bring a risk based approach to this industry. This was extended to the medical device sector through the ISO14971 Risk management standard. These were introduced partially to address the question of risk management and innovation and so were welcomed by the industry and FDA.
This risk based approach leveraged the ICH-Q8 standard which introduced, among other things, the concept of design space. A design space establishes parameters that have been demonstrated to provide quality assurance. Once a design space is approved, movements within it are not considered a change from a regulatory point of view. This creates a space within the agreed boundaries for innovation to occur.
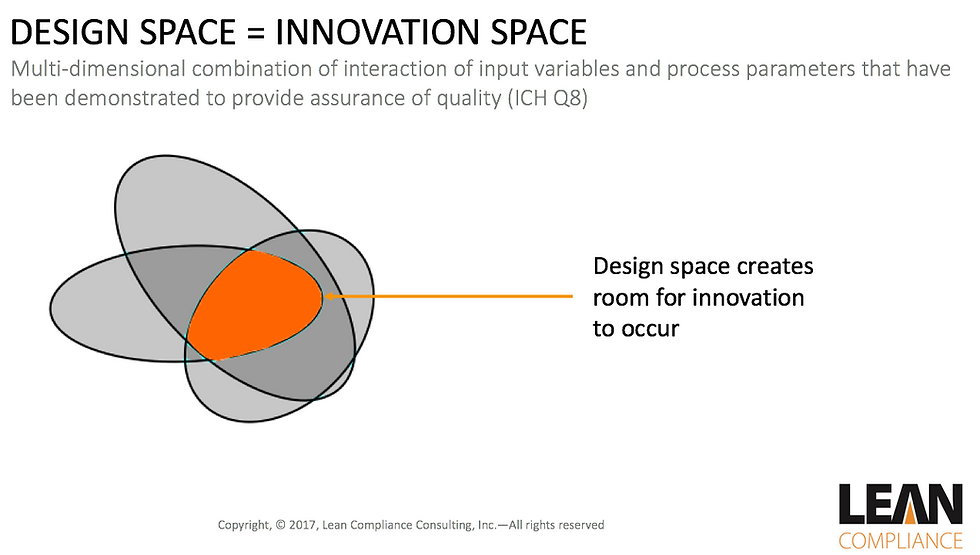
Now, let's consider the process sector where we discover a similar notion referred to as, "Replacement in Kind" or RIK. Replacement in Kind uses the idea that when changes are made to the "design basis" a Management of Change (MOC) process must be followed to manage risk. Otherwise, the change is considered a "replacement" and not a change from a regulatory point of view.
In many ways, RIK has the same effect that design space has in the Pharma/Med Device sectors. They both define boundaries that allow certain changes to occur that will produce the same design outcomes.
Unfortunately, one notable difference between the two is how design basis is currently managed in the process sector. Design information tends not to be as controlled or managed as it in the Pharma/Med Device industry. In fact, it is common in older facilities to find that the design basis is no longer even known and engineers and maintenance crews default to the manufacturer's specifications for the equipment, parts, or material replacements. This has the effect of reducing the options and innovations that might otherwise be available.
In a fashion, improving the management of design basis could allow for more innovation in the process sector. More changes could be considered as RIK without increasing risk. This would result in fewer MOCs and fewer resources being spent redoing hazard analysis, risk assessments and so on.
Companies need to innovate and at the same time "play it safe" when it comes to workers, the people around them, and the environment. This is not easy but necessary. Re-imagining the design change process may be a good first step to support more innovation and staying compliant both at same time.
Plan-Do-Check-Act Questions:
How important is innovation to achieving the outcomes your business has targeted?
What would it look like if more innovation could occur without increasing risk?
In what ways has compliance hindered innovation in your organization?
What steps could be taken to manage risk and increase innovation in operations and maintenance processes?