A Safety Management System for Everyone
- Raimund Laqua
- Feb 27, 2020
- 5 min read
Updated: Jun 9, 2020
Adopting a Safety Management System (SMS) has typically required significant resources, large teams, and expensive technologies and expertise to establish let alone achieve effectiveness at improving safety outcomes. While a SMS is considered an essential part of an effective safety program it remains for many companies a luxury they believe they cannot afford.

One reason that supports this belief is that the approaches used by large companies represent best practices and must be used for companies of smaller size, levels of risk, and complexities.
However, smaller companies may in fact be in a better position to adopt a SMS with less effort and lower costs by using different practices than larger organizations.
In this article, we will consider a case study involving a Land Reclamation company that chose to adopt both a quality and safety management system; something they needed to grow the business but thought they couldn't afford.
Case Study

I had the opportunity over the last year to work with an organization involved in land clearing, reclamation, and development. This is an asset intensive operation similar to infra-structure construction projects that involve multiple crews, heavy equipment, and interactions with land owners, the public, and the environment.
Management wanted to bid on larger projects which required that they have a quality management system in addition to safety. They had always been a company that valued quality and safety but now needed to formalize this as part of a combined managed quality and safety program. They could have taken a traditional approach with a focus on documentation and writing procedures which would have created for them greater administrative overhead among other things. Instead they took an agile and lean approach to meet their objective.
The process
The first step was to define and then create a Minimum Operational System (MOS) for an integrated quality and safety program (more information regarding this approach can be found here).
Our objective was to establish the processes essential to provide a working system as soon as possible so they could begin to learn how to continuously improve over time.
The combined system was modeled after ISO 9001 and ISO 45001 and supported regulatory obligations for safety in Ontario, Canada. The following practices where incorporated into the implementation of their MOS:
Management learned essential concepts for a managed quality and safety program.
Monthly management reviews were adapted to be proactive (are we making progress) rather than only being reactive (what have we done).
Processes and procedures were defined to include measures of conformance, performance and effectiveness.
Risk-based assessments were incorporated into all safety and quality critical processes.
Data measurement processes were defined for all critical to quality and critical to safety objectives.
Corrective and preventative actions (CAPA) were combined to form a single Continuous Improvement (CI) process.
Customer satisfaction (NPS) forms and workflows were added to support feed-back processes.
A real-time QMS / SMS portal was built using Office 365 to provide continuous status of productivity, safety, and quality.
The technical features of the system included:
Operator safety check-in using mobile phones to monitor personal safety in remote locations.
Drone and site photos are stored and marked-up in Office 365.
Operator logs collected and tracked in Office 365 using Microsoft Forms.
Microsoft Teams used for project collaboration - SOW, photos, risk assessments, communications, project specific PPE, hazards, etc.
Microsoft Forms and Flows for Continuous Improvement requests, approvals, and implementation.
Microsoft Planner was used configured as a Kan-Ban to track improvement actions coming from CI’s and Management Reviews.
SharePoint libraries used to house and support the management of QMS / SMS documents and manuals.
SharePoint Lists used to manage training requirements and records.
Metrics tracked and visualized using SharePoint.
The QMS / SMS and all associated information is available to employees and contractors from their phones and laptops.
The outcome
The introduction of an operational QMS / SMS during the year (rather than at the end) produced early benefits associated with:
Identification and removal of waste in the process
Improved safety and quality measures
Improved project measurements which led to improvements in project estimation
Improved engagement and participation with project teams and management
Installation of the quality and safety manager in their roles having learned essential behaviors and practices during the implementation
The result was an operational quality and safety program implemented and sustained through continuous improvement at a fraction of the effort and cost as other approaches. The company was now in a position to continually improve their programs having learning how to do so during its implementation.
All of this was accomplished over the course of 12 months utilizing the Lean Compliance Startup Model which is part of The Proactive Certainty Program. This program consists of weekly coaching and work sessions led by subject matter experts as needed to achieve program objectives.
Why you may be in a better position to implement a SMS
The following observations can be made from this case study and from other projects we have worked on over the years:
1. Larger organizations are slower to change and require greater effort when they do
Larger companies typically:
Have greater inertia and friction that needs to be overcome when adopting new programs and systems.
Require more management to maintain system operations and sustain continuous improvement.
Take longer and require more effort to change behaviors.
Smaller companies typically:
Have less inertia and friction to overcome which enables the adoption of new programs and systems sooner and with less effort.
Require less management to maintain system operations and sustain continuous improvement.
Can change behaviors faster with less effort.
In our case study the company was able to make decisions quickly, engage employees and contractors in participative collaboration, and adopt changes incrementally over the course of 12 months.
2. Larger companies are more likely to follow traditional implementation approaches
Traditional implementations use a reductive component-first approach that often leads to silos, overlapping responsibilities, duplication of effort, and other forms of waste. This approach is characterized by:
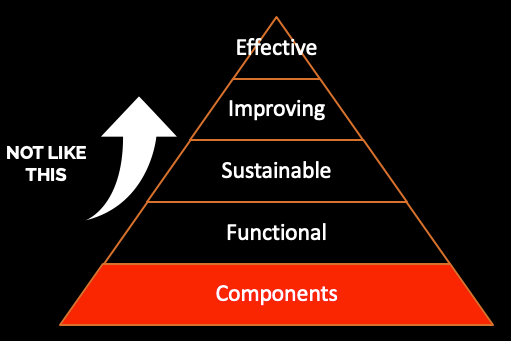
A focus on policies and procedures over outcomes
Reductive, divide and conquer approach
Removal of waste to address previous inefficiencies leaving less available for real improvements
Committees, large projects and waterfall methodologies
Viewing continuous improvement as the end game
However, a holistic systems-first approach leads to an integrative, more efficient, and the achievement of operational status sooner with less waste in the process. This approach is characterized by:

A focus on outcomes over non-value activities
Integrative, collaborative and participative approach
Adding capabilities to achieve better outcomes
Agile and lean teams with continuous delivery methodologies
Viewing continuous Improvement not as the end game but as the way systems are built
In our case study, a systems-first approach was used to establish a working system of essential processes to support a continuous delivery of quality and safety capabilities.
3. Technology is more abundant and available than ever
Advancements in digital technologies have provided companies of all sizes with low cost, on-demand, and more powerful capabilities that help to drive better safety outcomes:
The Cloud
Big Data
Internet of Things
Machine Learning and AI
Blockchain
And many others
The company in our case study leveraged Microsoft - Office 365 cloud platform to provide the technology for their QMS and SMS. This was affordable, secure, configurable, included automation support, and available on every device.
4. Reactive management requires greater effort to achieve better results
Larger companies tend to have baked-in management practices that reinforce the creation of waste in the form of excessive audits, reporting, and fixing things after the fact.
However, smaller companies can be more agile, have fewer fixed systems, and can be more proactive with their compliance.
In our case study, the organization was not weighed down needing to support reactive processes and behaviors. Their perspective was always forward looking and always proactive.
Conclusion
Companies of every size can benefit from having an operational SMS. Smaller companies can take advantage of their size along with agile / lean approaches to implement a SMS that they can afford. In fact, they may have an advantage over larger companies in that they can achieve operational status sooner and be more proficient at continuous improvement in the process.
To find out more about our lean approach to compliance visit www.leancompliance.ca.